Rotocaster
(Casting Silicone
Mold Bladders)
Bladder molding is an effective method for producing hollow composite parts, using an internal bladder to apply pressure against a female mold. While off-the-shelf tubular bladders work well for simple shapes, more complex geometries require custom bladders for uniform pressure distribution. Traditional bladder fabrication methods involve manual cutting, sealing, or painting silicone onto a mandrel, which can be labor-intensive and inconsistent. To streamline this process, I explored rotocasting as an automated solution for producing tailored bladders directly within the mold.
Project Definition
The goal was to develop an automated bladder fabrication process that eliminates the need for custom mandrels while ensuring consistent wall thickness and precise fit. The system had to be compatible with existing composite molding workflows and use off-the-shelf components or materials that could be produced in-house. Additionally, I sought to reduce labor time and improve bladder uniformity for complex molds.
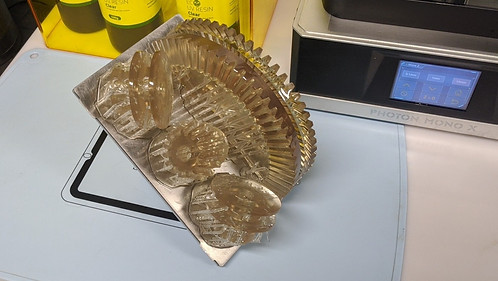
Project Design
I used CAD and CNC tools to design and build a rotocasting machine, a system commonly used for manufacturing hollow plastic parts. The frame was sized to accommodate a full front triangle mold, ensuring compatibility with large composite components. To keep costs low and accelerate development, I made gears using mSLA 3D printing for enhanced rigidity and precision. A variable-speed gearmotor controlled rotation speed, and interchangeable gears allowed for fine-tuned speed ratios between rotation axes. Extensive material testing was performed to identify the ideal silicone formulation and casting parameters for reliable bladder production.

Project Delivery
The final system successfully produced custom-shaped bladders with uniform thickness, ensuring consistent pressure application during composite molding. The ability to fabricate bladders directly within the mold eliminated manual trimming and construction errors, significantly improving process efficiency. While the approach proved viable, further refinement is needed to optimize silicone material selection and rotation speed calibration for more intricate geometries. Future improvements include exploring alternative casting materials and refining the automation process to enhance production scalability.
